Industrial machinery manufacturing focus: Why wait for the revolution?
Corcentric
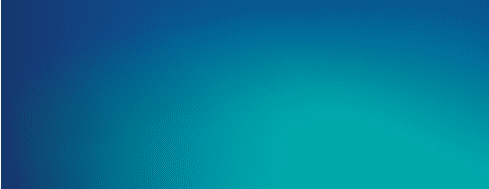
The industrial machinery manufacturing industry is worth hundreds of billions of dollars per year globally. The global construction equipment industry is worth almost $140 billion in itself, according to Statistia. It is likely that current growth rates of near double digits will continue throughout the 2020s, perhaps even accelerating in line with population growth.
The desire for improved efficiency has driven many changes across the manufacturing industry over the centuries. From the automation of weaving looms back in 1784 through the industrial revolution and on to today’s highly automated manufacturing processes.
There is now talk of Industry 4.0 and a new industrial revolution though. This is widely considered to be driven by the emergence, and adoption, of technologies such as 3D printing, artificial intelligence, augmented reality, and advances in material science (such as nanotechnology, graphene, and advances in metallurgy). How will this impact industrial machinery manufacturing and how can you balance investing in this against day-to-day cash flow challenges?
Digital transformation in the manufacturing sector
Many aspects of digital transformation in the manufacturing sector have been in place, to some degree, for decades. According to General Electric, in this article, additive manufacturing has been around for several decades, emerging from the combination of CAD, automation, and precursors of 3D printing, such as material extrusion, binder jetting, and sintering.
With advances in 3D printing and industrial automation, rapid prototyping, testing, and production of complex geometrical components is now commonplace amongst leading industrial machinery manufacturers.
As computer simulation technology has advanced, the concept of creating a digital twin has emerged. Initially this was seen as a more efficient way to test prototypes, but now many businesses see this as an essential part of the manufacturing process and product lifecycle. Digital twins can help manufacturers fine-tune the production process in real time and keep informed of the expected component performance throughout its lifecycle. Leveraging sensors and connectivity of the internet of things (IoT), digital twins can receive input from real world usage scenarios to identify problems before they occur, and carry out preventative maintenance.
It’s apparent from mergers and acquisitions over the last couple of years that many of the larger industrial machinery manufacturing companies are already on an IoT digitalization journey. Some high-profile examples are Hyundai Motor Company’s acquisition of Boston Dynamics, Siemens’ acquisition of IoT start-up Wattsense, and Rockwell Automation’s acquisition of cloud-based manufacturing solution provider Plex Systems.
Manufacturing companies have used robotics on the production line for decades, but this functionality continues to improve. The combination of feedback via IoT-enabled sensors, artificial intelligence to spot patterns and iteratively refine efficiency and performance and 3D printing and robotics to apply these refinements paves the way for greater and greater efficiency.
Industrial machinery manufacturing companies that are able to leverage the combination of these technologies, combined with access to the latest materials, whether metalworking, plastics or nanotechnology, are likely to be able to offer more compelling industrial machinery to their end customers, at more competitive prices.
Trends in equipment manufacturing
A recent top-5 trends report from the Association of Equipment Manufacturers (AEM) highlighted how workforce challenges, supply chain management, and leveraging data for improved traceability are all high on the agenda for equipment manufacturers in the US. Similar priorities can be seen globally.
Workforce challenges are not limited to equipment manufacturing, or manufacturing as a broader industry, but the combination of fewer candidates and the acceleration of technological progress in this industry will make recruitment and staff retention harder for some years.
However, aspects of technology adoption, such as augmented reality and improved remote connectivity over 5G, will allow for more flexible working practices in the equipment manufacturing industry, appealing to expectations of those seeking new roles as part of the great resignation.
Supply chain management is increasingly important as OEMs are required to comply with an ever-evolving number of standards, placing the onus on them to communicate with suppliers and ensure end-to-end compliance across the supply chain.
Traceability through improved data visibility has become a particularly important consideration for agriculture, as they are challenged with doing more with less.
“Data enables farmers to make better decisions for the year based on the 4R principle of right rate, right place, right time and right source. Thus, using historical data to make decisions on what to apply where and when.
“Farmers have been doing this for years, but with costs of fertilizer and other farm inputs on the rise, utilization of this data has never been more important. It can also help provide input into other areas of the farm to increase efficiencies there as well,” Austin Gellings, AEM agriculture services manager, said.
Even though we live in a world facing extensive climate change, the HVAC (Heating, ventilation, and air conditioning) market is predicted to expand less in the next few years (CAGR of 6.3% from 2022 to 2030) than the overall industrial machinery market (GAGR of 8.6% from 2022 to 2026). However, both look set to fair better than parts manufacture for Aerospace to Automotive markets.
Challenges in the industrial machinery manufacturing sector
The global market for industrial machinery manufacturing has endured the downtime from the coronavirus pandemic and supply chain crisis of 2022, but looks set to rebound as markets recover and life returns to normal.
Given the length of supply chains and manufacturing commitment in producing industrial machines, the rebound will take far longer than the recovery of the service industry in meeting rising end user demand.
These same characteristics of the industrial machinery manufacturing industry may also present a mounting cash flow challenge, as customers seek longer payment timeframes and extended credit. Without cash inflow, manufacturing cannot purchase raw materials and supply chain delays result.
As per the trends in equipment manufacturing and many other industries, workforce challenges are likely to pose a major challenge for industrial machinery manufacturers for some years to come. Remote working may be possible in a few aspects of manufacturing, but material handling, production-line maintenance, and many other aspects are unavoidably on-site activities.
Keeping pace with technological innovation is likely to present another significant challenge in this sector. High-quality output from competitors, at lower prices, will drive the need for greater investment in technology to improve efficiency and output quality and stay competitive. Combining this driver with workforce challenges could see greater reliance on automation and AI in the manufacturing process, but implementation will pose its own set of challenges.
With the advent of advanced materials, machine tools have to step up to the job. Harder alloys and tougher nanomaterials can’t be machined with traditional tools, so manufacturers will need to invest in tools as well as technology to get the most out of these new materials.
Accessing capital to invest in new technology
Industry leaders such as Caterpillar Inc. and General Electric with enormous market share face almost as much a challenge in investing proportionally in innovation as smaller industrial manufacturing businesses. The bigger the business, the bigger the investment needed.
However, liberating working capital from the accounts receivable ledger provides an opportunity to access cash proportional to the business size. The larger the business, the larger the AR ledger. At Corcentric, we enable businesses to bring their days sales outstanding (DSO) down dramatically and fix this at a lower number of days, permanently.
For instance, a business with income of £100m has £274k of working capital tied-up for every day of DSO. If the business reduced their DSO by 42 days, for example, this would equate to a liberation of £274k x 42 days, or £11.5m. So, a business with an average DSO of 57 days could liberate £11.5m of receivables by fixing their DSO at 15 days.
Corcentric already provides this service for many global businesses; you can see examples such as how we helped Daimler reduce their DSO from 37 days to 15 days and fix this at that level permanently.
Why wait for money already owed to your business, when this can be used to fuel the next industrial revolution now? Find out more about Corcentric’s Managed Accounts Receivable solution in this white paper, or reach out to one of our experts for a quick 1-to-1 discussion to see the value it could bring to your business as soon as next quarter.